Der DTC wird durch die Komponenten im internen Verstärker des ICP-Sensors festgelegt. In den Spezifikationen für die ICP-Kraftsensoren in diesem Katalog ist der DTC für jeden Kraftsensor aufgeführt.
Beim Testen mit ICP-Sensoren gibt es zwei Zeitkonstanten, die für die Bestimmung der Niederfrequenz berücksichtigt werden müssen. Die eine ist die des Sensors, die ein fester Wert ist, und die andere die der elektrischen Kopplungsschaltung, die im Signalaufbereiter verwendet wird.
Wenn ein ICP-Sensor einer Schrittfunktion unterworfen wird, wird eine Ladungsmenge Δq erzeugt, die proportional zum mechanischen Eingang ist. Nach dem Gesetz der Elektrostatik ist die Ausgangsspannung ΔV = Δq/C, wobei C die Gesamtkapazität des Sensorelements, des Verstärkers und des Messkondensators ist. Diese Spannung wird dann durch den MOSFET-Verstärker verstärkt, um die endgültige Sensorempfindlichkeit zu bestimmen. Nach dem anfänglichen Eingangsschritt fällt das Ladungssignal gemäß der Gleichung q = Qe-t/RC ab, wobei
q = momentane Ladung (pC)
Q = anfängliche Ladungsmenge (pC)
R = Wert des Vorspannungswiderstands (Ohm)
C = Gesamtkapazität (pF) t = Zeit nach t0
e = Basis des natürlichen Logarithmus (2,71 8)
Diese Gleichung wird auch in Abb. 6 unten grafisch dargestellt:
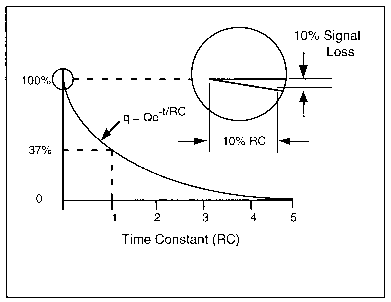
Abbildung 6: Standard-DTC-Kurve
Das Produkt aus R und C stellt die DTC (in Sekunden) des Sensors dar. Die Zeitkonstanten der Sensoren variieren von wenigen Sekunden bis zu >2000 Sekunden für Standardsensoren. Spezielle Zeitkonstanten können durch Ändern des Widerstandswerts R im eingebauten mikroelektronischen Verstärker des Sensors bereitgestellt werden.
Die meisten Auslesegeräte haben eine hohe Eingangsimpedanz, >1 Megohm. Bei diesen Systemen wird der Sensor-DTC, wie zuvor beschrieben, zum dominierenden Wert und kann zur Bestimmung der Signalentladungsrate verwendet werden. Bei Signalen, die an Auslesegeräte mit niedriger Impedanz (im Allgemeinen <1 Megohm) gekoppelt sind, muss jedoch die Systemzeitkonstante bestimmt werden. Dies wird im folgenden Abschnitt näher erläutert.