Nachdem das Sensorelement ein vermutlich gewünschtes Ausgangssignal erzeugt hat, muss dieses Signal aufbereitet werden, bevor es von einem Oszilloskop, Analysator, Schreiber oder einem anderen Auslesegerät analysiert werden kann. Wie in Abbildung 4 dargestellt, kann diese Signalverarbeitung auf zwei verschiedene Arten erfolgen: (1) intern im Sensor durch eine mikroelektronische Schaltung oder (2) extern am Sensor in einer "Black Box". (PCB verwendet die eingetragene Marke ICP® zur Bezeichnung von Sensoren mit eingebauter Mikroelektronik. Sensoren ohne Elektronik werden üblicherweise als Ladungsmodus-Sensoren bezeichnet).
Abbildung 4: Sensorsysteme
Diese analogen Verarbeitungsschaltungen haben dieselben allgemeinen Funktionen, nämlich: (1) Umwandlung in ein nützliches Spannungssignal mit niedriger Impedanz; (2) Signalverstärkung/-dämpfung; und (3) Filterung. Es ist jedoch wichtig zu beachten, dass die Position des Schaltkreises für den ordnungsgemäßen Betrieb des Sensorsystems entscheidend sein kann. Es folgt eine detailliertere Beschreibung der einzelnen Methoden.
Zunächst wird der ICP®-Sensor erörtert. Dieses Konzept hat seit seiner Entwicklung im Jahr 1967 ein hohes Maß an technischen Verbesserungen erfahren. Das heißt, die Schaltkreise sind kleiner geworden, die Preise für die Komponenten sind gesunken und die Signalverarbeitungsfähigkeiten haben sich durch integrierte Miniaturschaltungen und Mirco-Hi-Meg-Widerstände erhöht. Trotz dieser Verbesserungen bleibt die ursprüngliche Absicht der Idee unverändert: Einfachheit und Benutzerfreundlichkeit. Dieses Zweileitersystem verwendet einen gemeinsamen Leiter für Strom/Signal und einen zusätzlichen Leiter für die Signalmasse. Bei den eingebauten Schaltungen handelt es sich um Miniatur-Ladungs- oder Spannungsverstärker, je nach Art des Sensorelements. Die Stromversorgung dieser Komponenten erfolgt in der Regel über eine 18 bis 30 VDC, 2 mA Konstantstromversorgung. (Abgesehen vom Preis, der Bequemlichkeit und/oder den Funktionen gibt es keinen technischen Vorteil, wenn die Konstantstromquelle extern oder in das Auslesegerät eingebaut ist). Ein detailliertes Systemschema ist in Abbildung 5 dargestellt.
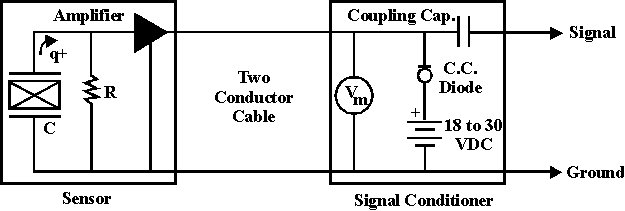
Abbildung 5: ICP®-Sensorsystem
Zu den Merkmalen dieses Systems gehören: (1) die eingebaute Mikroelektronik erzeugt ein Spannungssignal mit niedriger Impedanz, das mit den meisten Auslesegeräten kompatibel ist; (2) es wird nur ein einfacher, leicht zu bedienender Konstantstrom-Signalaufbereiter benötigt, was zu geringeren Kosten pro Kanal führt; (3) das Signal kann über lange Kabel ohne Verlust an Signalqualität durch raue Umgebungen übertragen werden; (4) die Betriebstemperatur des Schaltkreises ist in der Regel auf 250 F (121 C) oder manchmal 325 F (154 C) begrenzt; (5) er funktioniert mit gewöhnlichen zweiadrigen Koaxial- oder Twisted-Pair-Kabeln; und (6) die Eigenschaften des Sensors (Empfindlichkeit und Frequenzbereich) sind im Sensor festgelegt und unabhängig von der Versorgungsspannung.
Charge-Mode-Sensoren verwenden dieselbe mechanische Sensorstruktur wie ICP®-Sensoren, die Signalverarbeitungselektronik ist jedoch extern untergebracht. Da integrierte Mikroschaltungen noch nicht entwickelt worden waren, arbeiteten die ersten piezoelektrischen Sensoren, die in den 1950er Jahren entwickelt wurden, nach diesem Prinzip. Diese Aufladesysteme waren oft schwierig zu bedienen und aufgrund des aufwendigen externen Ladungsverstärkers traditionell teuer. (Alternative, kostengünstigere Inline-Geräte werden immer beliebter.) Heute werden Ladungsmodus-Sensoren in der Regel nur noch in Umgebungen eingesetzt, in denen die Temperatur die Verwendung von Sensoren mit eingebauter Elektronik verbietet.
Wie nicht anders zu erwarten, bieten Ladungsmodus-Systeme verschiedene Vor- und Nachteile, darunter: (1) der Sensor gibt ein hochohmiges Signal aus, das vor der Analyse aufbereitet werden muss; (2) ein externer Signalaufbereiter ist erforderlich (Labor-Ladungsverstärker, Inline-Source-Follower usw.)); (3) das hochohmige Signal kann durch Umwelteinflüsse wie Kabelbewegungen, elektromagnetische Signale und Hochfrequenzstörungen verunreinigt werden; (4) da die Elektronik extern ist, können bestimmte Modelle bei Temperaturen bis zu 540 C (1000 F) betrieben werden; (5) es ist eine spezielle rauscharme Verkabelung erforderlich; und (6) die Eigenschaften des Sensors (Empfindlichkeit und Frequenzbereich) sind variabel und können durch Umschalten von Komponenten im externen Signalaufbereiter verändert werden.