Le DTC est fixé par les composants de l'amplificateur interne des capteurs ICP. Les spécifications des capteurs de force ICP présentées dans ce catalogue indiquent le DTC de chaque capteur de force.
Lors des essais avec les capteurs ICP, deux constantes de temps doivent être prises en compte pour la détermination des basses fréquences, l'une étant celle du capteur qui est une valeur fixe, et l'autre celle du circuit électrique de couplage utilisé dans le conditionneur de signaux.
Lorsqu'un capteur ICP est soumis à une entrée de type step function, une quantité de charge, Δq, est produite proportionnellement à l'entrée mécanique. Selon la loi de l'électrostatique, la tension de sortie est ΔV = Δq/C où C est la capacité totale de l'élément de détection, de l'amplificateur et du condensateur de mesure. Cette tension est ensuite amplifiée par l'amplificateur MOSFET pour déterminer la sensibilité finale du capteur. Après l'entrée du pas initial, le signal de charge décroît selon l'équation q = Qe-t/RC où :
q = charge instantanée (pC)
Q = quantité initiale de charge (pC)
R = Valeur de la résistance de polarisation (ohms)
C = capacité totale (pF) t = temps après t0
e = base du logarithme naturel (2,71 8)
Cette équation est également représentée graphiquement à la figure 6 ci-dessous :
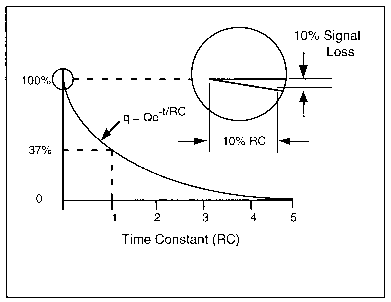
Figure 6 : Courbe DTC standard
Le produit de R et C représente le DTC (en secondes) du capteur. Les constantes de temps des capteurs varient de quelques secondes à plus de 2000 secondes pour les capteurs standard. Des constantes de temps spéciales peuvent être fournies en modifiant la valeur de la résistance, R, dans l'amplificateur microélectronique intégré au capteur.
La plupart des instruments de lecture ont une impédance d'entrée élevée, >1 Mégohm. Pour ces systèmes, le DTC du capteur, tel que discuté précédemment, devient la valeur dominante et peut être utilisé pour déterminer le taux de décharge du signal. Cependant, pour les signaux couplés à des dispositifs de lecture à faible impédance, généralement <1 Mégohm, il est nécessaire de déterminer la constante de temps du système. Ceci sera expliqué plus en détail dans la section suivante.